A realistic flame model has been set up through finite-elements model (FEM) software inside HITCOMP European project
- Inicio
- Investigación y transferencia
- Grupos de investigación
- HITCOMP: High Temperature characterization and modelling of thermoplastic composites
- A realistic flame model has been set up through finite-elements model (FEM) software inside HITCOMP European project
In order to simulate the fire tests carried out on AIRBUS premises (Getafe, Spain), LIR-UC3M is developing a simulation model that allows to predict the thermal behaviour of a flat and thin thermoplastic plate under high temperature thermal excitation (fire) on one of its sides (called hot side). To that end, a software based on finite elements model (FEM) is employed.
The referred simulation model has a flame model as main input adapted to simulate the effects caused by a real flame under ISO:2685:1998 standard on the plate hot side. LIR-UC3M has consolidated the flame model by using a 3D normal distribution temperature map on the thermoplastic surface. This distribution increases the temperature values until a steady-state is reached.
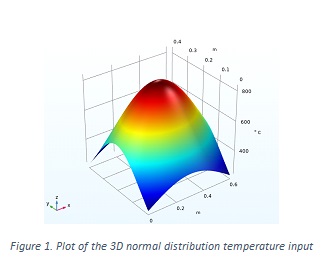
On the other hand, due to the fact that the fitting and its corresponding attached rivets (known as hiloks), located at the plate hot side are metallic, the surfaces exposed to the flame are simulated with spatial constant high temperature that increases with time respect to the maximum temperature value.
Flame model gif
